Keeping your trucks running smoothly isn't complicated. The key lies in routine inspections, identifying issues early on, tracking fleet health, and adopting prevention-focused strategies. Scheduled checks and fixes secure optimal uptime, enhanced productivity, and safety. Expert guidance from experienced technicians will guide you through fleet maintenance through the effective use of tech solutions, thorough record-keeping, and qualified team members. Dive into this complete guide to fleet maintenance and open the door to cost-effective operations. There's plenty to learn and understand!
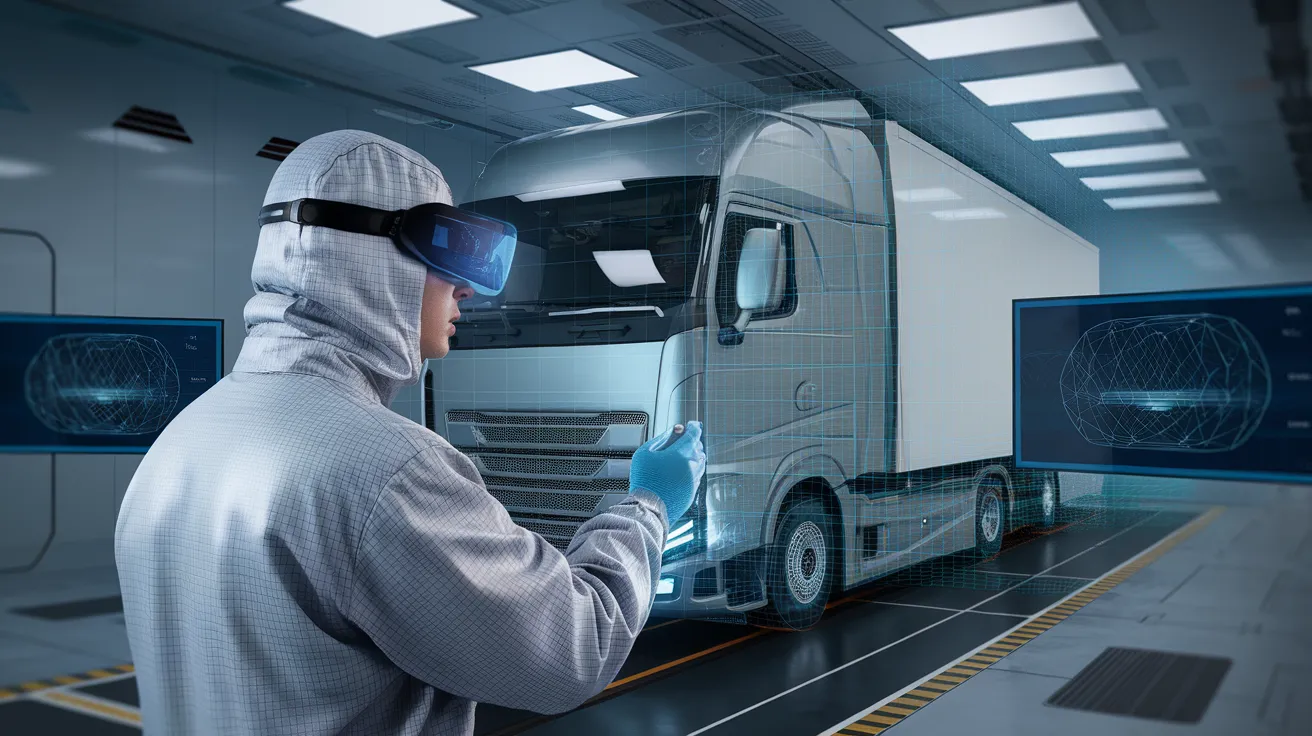
Main Insights
Recognizing the Significance of Scheduled Fleet and Truck Maintenance
Though it could feel overwhelming, mastering proper fleet and truck maintenance is vital for every prosperous company. The benefits of maintenance greatly surpass the resources you put in. Regular checks and servicing can greatly increase your vehicles' longevity, avoiding hefty replacement costs. Moreover, there's an obvious relationship between well-maintained trucks and improved fuel efficiency. This means lower fuel costs, enhancing your total operational efficiency. Moreover, routine servicing can uncover minor concerns before they become serious problems, preventing costly repairs down the line. Thus, never discount the value of routine maintenance; it can be a significant factor for your business's bottom line.
Identifying Fundamental Parts of a Effective Upkeep System
To ensure your fleet's efficiency and durability, it's essential to recognize the fundamental aspects of a successful maintenance program. You'll must comprehend the essential elements of maintenance, monitor the condition of your fleet periodically, and implement preventive measures ahead of time. With these in place, you're positioned to decreasing downtime and optimizing productivity.
Essential Program Maintenance Requirements
When it comes to boost your fleet's efficiency and lifespan, implementing a solid maintenance program is vital. Key components of the program consist of periodic inspections, regular servicing, and anticipatory repairs. Each of these elements plays a crucial role in preventing expensive failures and decreasing downtime. While the benefits of a maintenance program are numerous, don't ignore the setup hurdles. These may include logistical issues and staff resistance. However, with careful preparation, clear communication, and dedication to training, these barriers can be surmounted. Don't forget that an well-designed maintenance program isn't just about repairs; it stops them from occurring. It's an investment in your fleet's future – and it's one that delivers substantial benefits.
Fleet Health Monitoring
As you explore the fundamentals of a effective maintenance program, recognizing the critical role of fleet condition monitoring is essential. It goes beyond maintaining operational vehicles, it focuses on maximizing fleet performance. Monitoring technologies provide a complete view of your fleet's health, allowing you to identify potential issues before they escalate.
Such tracking solutions monitor vital parameters like fuel consumption, tire health, engine status, and more. By utilizing this data, you're not only ensuring the durability of your fleet but also reducing unnecessary repair costs. Remember timely discovery is crucial in fleet management. So, invest in dependable monitoring technologies and keep ahead of the curve. Don't merely address problems, predict them. Monitor your fleet's status regularly and your operation will perform optimally.
Setting Up Preventive Strategies
Although tracking your fleet's condition is crucial, implementing preventive measures is equally important to maintain a successful maintenance program. It's important to identify potential issues before they develop into major repairs and equipment downtime. Let's explore preventive maintenance approaches.
One effective measure is establishing a comprehensive maintenance checklist. This checklist should outline all necessary inspections, tune-ups, and parts renewal. Periodic engine inspections, tire servicing, and oil changes are essential. However, remember to check basic components like windshield wipers, lighting systems, and filtration systems.
Your checklist should also include a schedule for each task. Adhering to this timeline ensures that your fleet remains in peak condition. Keep in mind, preventive measures saves costs, time, and troubles in the future.
Important Periodic Checks for Truck and Fleet Maintenance
To ensure your vehicles continue to be in peak condition, you should focus on regular maintenance checks. These inspections encompass scheduled maintenance inspections and critical component assessments. By maintaining these essential procedures, you'll increase your fleet's longevity, enhance operational performance, and consequently, save on major repair expenses.
Planned System Examinations
Scheduled maintenance checks are your strongest line of defense from unplanned vehicle and fleet malfunctions. This maintenance gives you a chance to identify and resolve problems before they escalate into major repairs or hazardous situations. One of the most significant advantages of regular maintenance is the reduction of operational delays, which can significantly affect your operation's performance and revenue.
Vital Component Assessments
Following up on the critical nature of scheduled maintenance inspections, let's examine the key essential component checks that should be conducted regularly to maintain maximum truck and fleet performance. First examine the brake system – ensure all components are operating correctly, from brake pads to fluid levels, while also checking for leaks. When overlooked, brakes might fail, leading to devastating incidents. Tire pressure checks are equally important. Underinflation raises fuel consumption and tire wear, while over-inflation may lead to a blowout. Invest in a high-quality pressure gauge for exact readings. Remember tires should be cold during checks for optimal results. Regularly performing these essential checks can help avoid costly repairs and potential accidents. Maintain safety on the road.
Essential Fleet Maintenance Practices for Peak Performance
In fleet management, it's crucial that you prioritize preventative maintenance to maintain peak efficiency. Establishing a comprehensive preventative scheduling system is key. This reduces unnecessary wear and tear, and lowers the chances of unscheduled downtime. You should schedule regular inspections and maintenance based on mileage, time, engine hours, or fuel used. Remember each vehicle is different and could require a personalized approach.
Maintenance training is another vital strategy to secure peak efficiency. Provide your staff with the required skills to detect potential issues early on. This saves both time and effort but also reduces costs. The combination of preventative scheduling and maintenance training will lead to a highly effective and trustworthy fleet. Prevention is always better than cure.
Key Advice for Fleet and Truck Maintenance and Recovery
Although vehicle fleet repair and restoration might appear challenging, grasping the fundamentals makes it easier. The first thing you should do should be to familiarize yourself with different maintenance methods. This expertise will allow you to spot issues effectively and promptly. Next, prioritize restoration projects based on the extent of repairs needed and the truck's function in your vehicle lineup. Regularly inspect each vehicle for potential issues and fix them immediately to avoid additional problems. Keep in mind, restoration isn't just about fixing issues, it's about improving the unit's efficiency and durability. Finally, always use high-quality parts for repairs; they'll offer superior longevity and function. Remember these guidelines, and you'll handle fleet maintenance and renovation effectively.
Harnessing Sector Developments for Cutting-Edge Fleet Management
To remain competitive in the trucking industry, it's essential to harness cutting-edge technologies for enhanced fleet maintenance. Technological advancements are transforming the maintenance landscape. Implement data analytics to track your fleet's operations and anticipate maintenance needs before they occur.
Modern tracking solutions keep read more track of engine health and efficiency, fuel consumption, and operator performance. Make use of these insights to plan proactive maintenance, minimizing costly operational interruptions.
Make sure to implement software updates. These updates typically provide important fixes and improvements that enhance your vehicles' safety and performance. Remember fleet maintenance extends past routine maintenance. You're working in a digital age, and adapting to sector developments will help ensure your fleet's durability and success. By implementing proper procedures, you will decrease expenses and effort, and potentially save lives.
Frequently Asked Questions
What Credentials Do You Need for a Qualified Commercial Fleet Technician?
You'll need a valid certification, meeting the standards of an accredited mechanic institution. Moreover, you require a comprehensive skill assessment, demonstrating your competency in different areas of fleet repair and maintenance. Prior experience is essential!
How Often Should Fleet Vehicle Tires Be Replaced?
As the seasons change, you should regularly check your fleet's tire wear periodically. Yet, it's typically best to replace tires every three to six years, based on driving conditions and frequency of use.
How Can You Identify Engine Issues in Trucks?
You'll spot truck engine problems by indicators including unusual engine noise or even decreased fuel efficiency. You may also notice unusual exhaust smoke, oil leaks, or possibly an illuminated check engine light that persists.
How Does Technology Impact Truck and Fleet Maintenance?
Technology is fundamental in enhancing truck maintenance. Advanced monitoring provides real-time data, while smart systems anticipate issues before they occur. You'll notice less vehicle downtime, enhanced security and ultimately, cost savings. It's a game-changer.
How Do Maintenance Needs Vary Across Fleet Vehicle Types?
Various vehicles need distinct maintenance schedules. You need to consider the vehicle's function, load capacity, and terrain type, as these aspects substantially impact required servicing. Always adjust maintenance specific to the type of vehicle.
Conclusion
Ultimately, the key is ensuring your fleet operates efficiently, right? Consistent upkeep isn't optional, it's a must. By recognizing critical parts, carrying out systematic evaluations, using preventative strategies, and harnessing industry innovations, you're doing more than basic maintenance, you're developing a high-performance fleet. And remember, truck and fleet repair isn't a failure, it's a pathway to enhancement. Stay committed, and you'll see your fleet's performance, dependability, and durability achieve new levels.